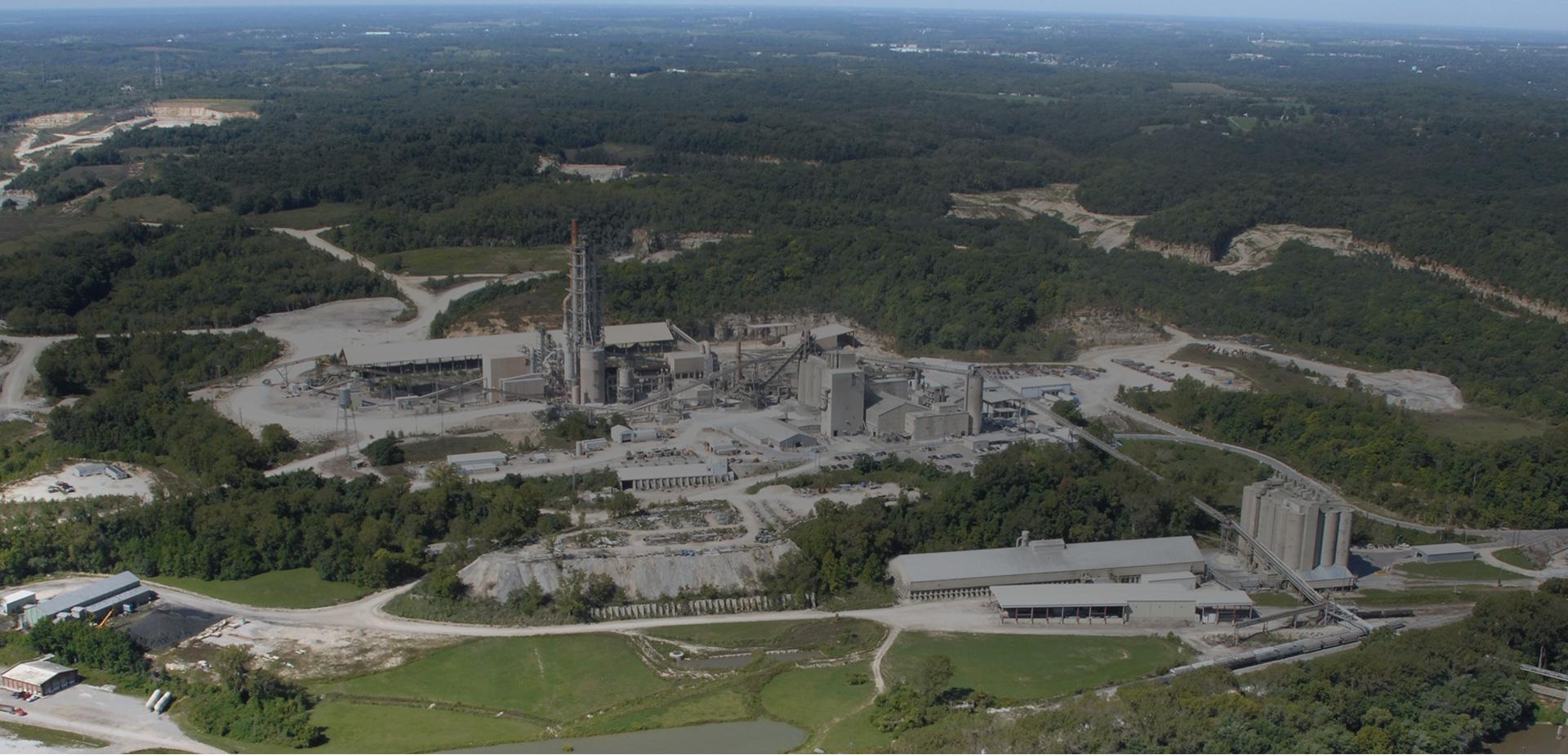
Quarry
Step 1: Quarry
For its raw materials, cement manufacturing uses minerals containing the four essential elements for its creation: calcium, silicon, aluminum, and iron. Most plants rely on a nearby quarry for limestone. The most common combination of ingredients is limestone coupled with much smaller quantities of clay and sand. Other raw materials, such as mill scale, shale, bauxite and fly ash, are brought in from outside sources when necessary. Rock blasted from the quarry face is transported to the primary crusher, where chair sized rocks are broken into pieces the size of baseballs. Some plants will use a secondary crusher, depending on process needs.
HOVER OVER ME
CLICK ME
Proportioning
Blending & Raw
Grinding
Step 2 : Proportioning Blending & Raw Grinding
The raw materials are analyzed in real-time using cross-belt analyzers and in the plant laboratory, blended in the proper proportion, and then ground even finer. Plants grind the raw materials with heavy, wheel-type rollers that crush the materials into powder against a rotating table. After grinding, the material is known as raw meal and is now ready for the preheater tower.
Preheater
Tower
Step 3 : Preheater Tower
The preheater tower supports a series of vertical cyclone chambers through which the raw meal passes on its way to the kiln. To save energy, modern cement plants preheat the meal before it enters the kiln. Rising more than 350 feet, hot exit gases from the kiln and clinker cooler combined with fuels such as ground coal, petcoke, natural gas, and recycled waste streams, heat the raw materials as they swirl through the cyclones.
Distribution
Step 7 : Distribution
From the grinding mills, the cement is conveyed to silos where it awaits shipment. Cement is shipped by trucks, rail, or barge.
Finish
Grinding
Step 6 : Finish Grinding
The clinker is ground in a ball mill—a horizontal steel tube filled with steel balls. As the tube rotates, the steel balls tumble and crush the clinker into a super-fine powder. It can now be considered Portland cement. The cement is so fine it will easily pass through a sieve that is fine enough to hold water. A small amount of gypsum is added during final grinding to control the set.
Clinker
Cooler
Step 5 : Clinker Cooler
The clinker tumbles onto a grate system cooled by forced air. Once cooled the clinker is ready to be ground into the gray powder known as Portland cement. To save energy, heat recovered is recirculated back to the kiln and preheater tower.
Kiln
Step 4 : Kiln
Raw meal now enters the huge rotating furnace called a kiln. It’s the heart of the cement making process—a horizontally sloped steel cylinder, lined with firebrick, turning approximately four revolutions per minute. The kiln is the world’s largest piece of moving industrial equipment. From the preheater, the raw meal enters the kiln at the upper end. It slides and tumbles down the kiln through progressively hotter zones toward the flame. At the lower end of the kiln, fuels such as ground coal, petcoke and natural gas feed a flame that reaches 3400 degrees Fahrenheit—one third of the temperature of the sun’s surface. Here in the hottest part of the kiln, the raw meal reaches about 2700 degrees Fahrenheit and becomes partially molten. This intense heat triggers chemical and physical changes. Expressed at its simplest, the series of chemical reactions converts the calcium and silicon oxides into calcium silicates, cement’s primary constituent. At the lower end of the kiln, the raw meal emerges as a new substance: red hot particles called clinker.
How Cement is Made
Cement is made from common materials such as limestone, clay, silica, and iron ore that are blended together.
Click on the circles above and tour Continental Cement’s Hannibal plant to view the cement making process.
For a more detailed description of the cement manufacturing process, visit Portland Cement Association’s presentation.